MM STONE REPAIR USER GUIDE & DATA SHEET
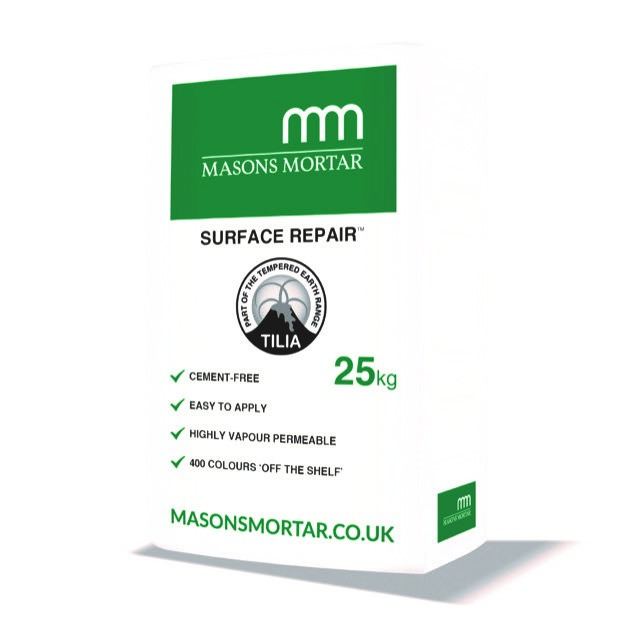
1.Product description
Mineral dry bagged masonry restoration repair mortar. Completely cement free lime binders and special aggregates.
2.General application and uses
MM Stone Repair Mortar – For partial or full surface repair of weathered or damaged sandstone or limestone where a strong bond and the ability to shape on hardening or when fully set is required. Can be tooled and finished to match the original, whether single or multiple colours.
3.Material Properties @ 28 days
- Bulk Density 1.420g/cm3
- Water demand 4.5- 5L per 25KG
- Open time 90mins
- Compressive strength <7.5 N/mm2
- Tensile strength <1.5 N/mm2
- Modulus of Elasticity 9000 MPa
- Vapour permeability 0.75-8 gxm2xhx mmHg
4.Application instructions
Ambient and materials / surface temperature range to be within +50C to +300C Out with these ranges consult our technical department.
5.Background / substrate preparation
- Cut back surface to remove defective masonry, to a sound base using a toothed chisel.
- If repairing only part of a unit, cut edges to straight lines on flat work, ellipses on curved work. Use of cutting discs is recommended to form sharp back chamfered edges.
- Where straight or ellipse line work is not possible, ensure MM Stone Repair Mortar does not finish to a thin feather edge – Where a feathered edge is unavoidable, the minimum edge thickness should be at least 5mm and once the repair is fully set (minimum 36 hours).
- All backgrounds must be free of salts, dust, loose or friable materials.
- Clean surfaces with mild grit blasting, pressure washing, and/or brushing with a stiff bristle brush. Use Biocide if required.
- Dampen, to control suction by pre-wetting if required.
- No standing water, remove with a sponge
6.Mixing
- For best results use hand held drill or whisk type mixer. Mix dry powder into water gradually, start wet, work to drier consistency. Do not short mix. Short mixing requires greater water content and will lead to bleed or shrinkage. Over mixing will weaken the material. Mix for 3-4 minutes with suitable mechanical means. If hand mixing, mix only small amounts and ensure the materials are properly mixed, usually around 4-5 minutes of vigorous mixing.
7.Application (one or multiple coats)
- Apply an initial layer 3mm or so with some pressure to the background, pressing materials into all grooves and tooling, then lay the rest of the MM Stone Repair Mortar up against this, wet on wet, to the desired thickness. In many instances various deeper sections should be filled first and brought to the level of the next deepest section, and so on, until the entire depth is filled. Remove any laitance between layers.
- Generally, up to a maximum of 40mm can be applied in a single application, or thicker in multiple passes. If form work is being used, or on flat or nearly level supports, work can be filled or laid up in a single pass.
- If filling in hanging layers, allow time for initial stiffening to take up before applying next layer, particularly if free forming projections and the like. Work must always be applied green on green for continuous application. If the sub base skins over (forms a laitance layer), scrape back to form a key before applying more MM Stone Repair Mortar.
- Ensure the final application is at least 1mm proud of the finished surfaces to allow for tooling – scraping, shaping back.
8.Finishing
- Finish with appropriate tools as the mortar takes its initial set, 8-12 hours depending on ambient conditions, (may be overnight in colder weather).
- Shaping with trowel edges, sculpting tools, sanding blocks, tungsten and the like can be done from 8 to 24 hours. For uniform perfect colour across all the repairs, the method of finishing and timing should remain consistent. Reinstate any mortar joints. MM Stone Repair Mortar must not bridge live cracks or mortar joints.
- All repairs should be overfilled and cut back. Where a tight, closed down finish is required, scrape back and close down lightly with a stainless-steel float without creating laitance while still sufficiently green to achieve the desired results. Over working can lead to fine laitance spider crazing on hardening.
9.Consumption (Approximate)
- 12.5 KGs per M2 at 10mm thick
10.Clean up
- Wash tools with clean water immediately after use.
11.Coloured (Pre-blended) or Colourpack™
- As supplied, either through coloured or with a Colourpack™ for onsite mixing.
- Through coloured dry bagged product, take materials as required and mix with water, colour will remain consistent throughout the depth of the material.
- Colourpacks are supplied for mixing with 6.25KG, 12.5KG and 25KG units of uncoloured MM Stone Repair Mortar.
- Empty the Colourpack™ into 75% of the mix water in the mixing bucket, turn package inside out and clean off any residual powder, stir with the drill whisk to distribute the Colourpack™ and mix in dry bagged mortar, adding water as necessary until a uniform, satisfactory mortar consistency is achieved. Not less than 3 minutes, not more than 4 minutes mixing time with a drill mixer.
- Proper protection must be maintained throughout the curing process. Colour variation will occur if differential hydration takes place. After placing, keep work protected from impact, strong sunlight, drying winds, rain and frost until properly cured.
Hazardous substances classification
- R 38: Irritating to the skin
- R 41: Risk of serious damage to the eyes
- S 2: Keep out of reach of children
- S22: Do not breathe dust
- S24/25: Avoid contact with skin and eyes
- S26: In case of contact with eyes, rinse immediately with plenty of water and seek medical advice
- S37/39: Wear suitable gloves and eye / face protection
- S46: If swallowed, seek medical advice immediately and show this container or label
Transport Hazard Class
N/A
Disposal
EC waste code no 170101
Any residue must be emptied out of bags or containers before recycling.
Solidify any residual material with water and after consulting the relevant authorities, dispose of in a construction material landfill site.